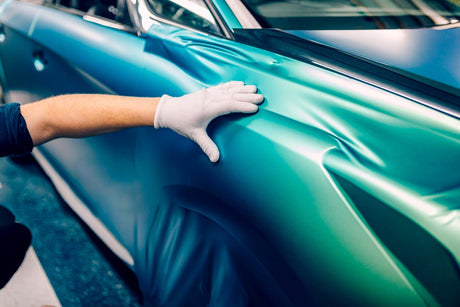
Common Causes of Vinyl Adhesion Failure
Avoid Car Wrap Lifting & Peeling – Get a Flawless Finish Every TimeDIY vinyl wrapping can be challenging, and adhesion failure is one of the most common issues. From poor...
Avoid Car Wrap Lifting & Peeling – Get a Flawless Finish Every TimeDIY vinyl wrapping can be challenging, and adhesion failure is one of the most common issues. From poor...
Here are the 10 non-negotiable skills for flawless vinyl film & PPF wraps. From bubble-free seams to contour mastery… How many have you truly checked? Level up in minutes! The...
Car wrapping has exploded in popularity, offering a dynamic way to personalize vehicles. But what happens when the canvas isn't pristine? Can you successfully wrap a car with rust or...
Wrapping a car in vinyl during winter can be challenging due to cold temperatures, but with the right preparation and tools, you can still achieve a professional finish. Work in...
Tired of fumbling with vinyl cuts that bring unsightly color splotches or wasted material? Ready to take your car wrapping game to the next level? Let's dive into some pro...
Wrapping your car's hood is a popular way to customize its appearance without committing to a permanent paint job. While it can be challenging, following a structured approach can help...
Protecting Your Investment Car wraps are a fantastic way to give your vehicle a unique look while protecting its original paint. But even with a wrap, your car's exterior still...
A flawless car wrap is the result of meticulous application and careful preparation. Unfortunately, many installers overlook crucial details that can compromise the final result. Here are some common mistakes...
Ever loved a car wrap but dreaded the removal process years later? We've all been there. Removing high-adhesion vinyl can be a time-consuming nightmare. But fear not, fellow car wrap...
It is hard to avoid stretching a vinyl film during an application, as there are compound curves and recessed areas, especially when you have to bridge the material and feed...
Forget the limitations of flat textures! Gloss vinyl wraps offer a surprisingly effective way to create a stunning 3D effect on your car. Here's the secret: embossing.Embossing adds a touch...
Color shift vinyl wrap film shows various colors in one finish from different angles or with different lights. It is wild enough to express your personality fully. But beauty does...
Sometimes, a wrap finish can fail not because of how you install it but how you approach it during the application: Wrong tools, thoughtless preparations, or incomplete cleaning… These can...